低高度経済は爆発的に成長している。
ドローンかつては高級玩具とみなされていたが、現在では様々な業界で活躍している。農薬散布、地形測量、都市部への食料配達、災害救助...
さらに、継続的に拡大しています。低高度経済の応用シナリオは近い将来、爆発的な革新を経験すると予測されます。材料の観点から見ると、すべての用途に単一のベース材料に依存するのは非現実的であることは明らかです。それでは、中国航空航天学会が発表した最新の「低高度経済シナリオ白書」を見てみましょう。様々な低高度シナリオにおけるベースマテリアルの選択がどのように異なるのか、そしてどのマテリアルが低高度経済に大きな影響を与えるのかを探ります。金属とプラスチック:どちらが良いでしょうか?ドローンや eVTOL を例に挙げると、人や物の輸送、物流、観光、農業など、用途を問わず、低高度航空機に使用される材料は、次の主要な物理的特性要件を満たす必要があります。軽量: 密度と質量が低いため、積載量と飛行耐久性が向上します。機械性能: 飛行時のストレスや振動に耐える高い剛性、強度、耐衝撃性。耐候性: 紫外線耐性、広い温度許容範囲 (-40°C ~ 80°C)、湿度に対する耐性。耐食性: 油および塩水噴霧腐食に対する耐性。加工性: 流動性が良好で、製造および組み立てが容易です。難燃性: UL94 V-0 または V-2 規格に準拠 (特に乗客用または物流用ドローンにとって重要)。費用対効果: 全体的な材料および製造コストは制御可能である必要があります (ハイエンドのアプリケーションではより柔軟性が許容されます)。厳しいパフォーマンス要件を超えて、軽量化あらゆる業界で競争上の目標となっており、これは航空機業界で特に当てはまります。低高度分野の初期段階では、高強度、高硬度の金属が主力材料として主流でした。例えば、アルミニウム合金金属界の「軽量チャンピオン」と称されるチタンは、密度がわずか2.7g/cm³と、鋼鉄より30~50%軽量です。優れた耐食性と表面処理後の長期耐久性に加え、適度な加工性と適度なコストも備えています。もう一つの例はチタン合金しばしば「高性能素材の獣」と称される。1200MPaを超える引張強度を有し、高温下でも優れた性能を維持し、酸、アルカリ、塩水噴霧といった過酷な条件にも耐えうる。しかし、金属素材にはよく知られた欠点があります。まず第一にコストです。例えばチタン合金は高価で加工が難しく、生産コストを押し上げます。さらに重量の問題もあります。金属部品は重いため、飛行距離と機敏性が低下し、複雑な低高度環境での航空機の効率的な操縦が困難になります。今日の効率化と軽量化の時代では、かつては信頼性があったこれらの材料は時代遅れになり始めています。では、低密度と軽量という本来の利点を持つプラスチックは、この課題に適うのでしょうか?結論を急ぐのではなく、必要な材料特性に基づいて、市場で主流のプラスチックベースの材料を調べたところ、次のことがわかりました。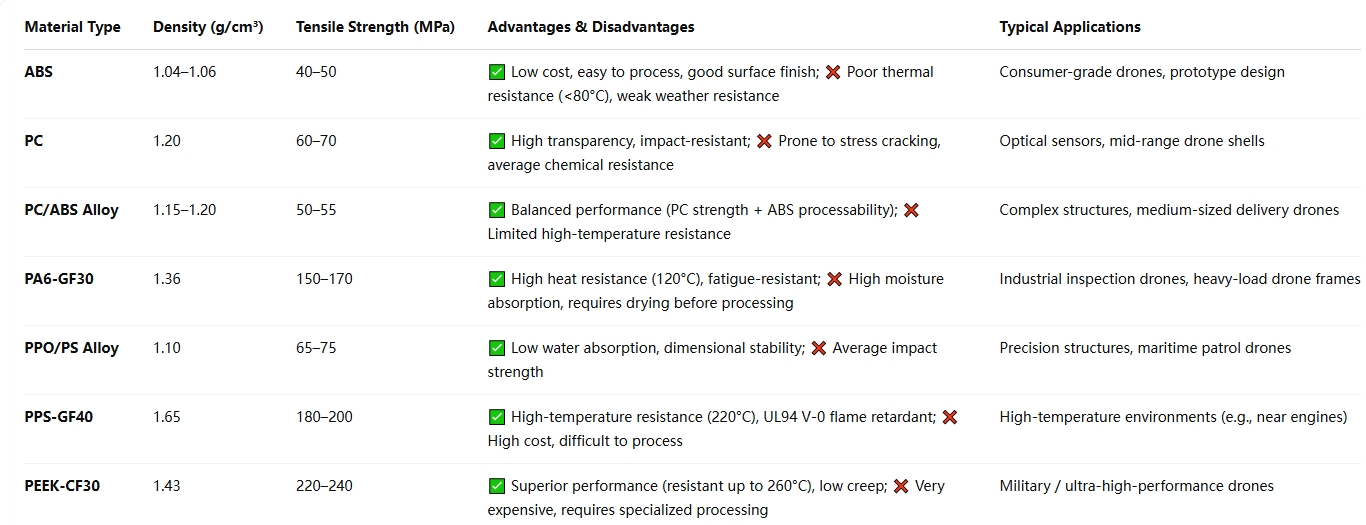
低高度経済の多様性は、様々な航空機がそれぞれ異なる飛行シナリオで運航することを意味します。その結果、求められる材料特性は具体的な用途によって異なります。そこで、次の記事では、さまざまなシナリオに合わせた材料選択ソリューションについて詳しく見ていきます。